Design Process
Brief definition
The project aims to develop an innovative accessory that caters to the needs of today's tech-savvy filmmakers and content creators. The accessory will seamlessly integrate with popular consumer devices, such as smartphones and APS-C cameras, with interchangeable lenses and filters while elevating the users' creative potential worldwide.
The goal is to enhance the filmmaking experience and capabilities of both amateur enthusiasts and seasoned prosumers. These people value functionality, usability, and innovation in their equipment and enjoy seamless integration with existing filmmaking tools and software. They are familiar with both consumer and prosumer gear but may not possess the expertise of professional filmmakers.
Research
The research phase commenced by systematically identifying various fields within photography and filmmaking. Through a blend of online investigation and interviews with amateur photographers, a comprehensive list of over 20 distinct fields emerged, each accompanied by its unique equipment requirements and common pain points faced by practitioners. These fields were then categorized based on the nature of the captured subject (static or dynamic) and the shooting environment (in-studio or on-location), streamlining the process of recognizing shared equipment needs across different domains. Subsequently, specific fields and their associated pain/gain points were carefully selected as most pertinent to the project's objectives, with detailed documentation provided in Figure 1.
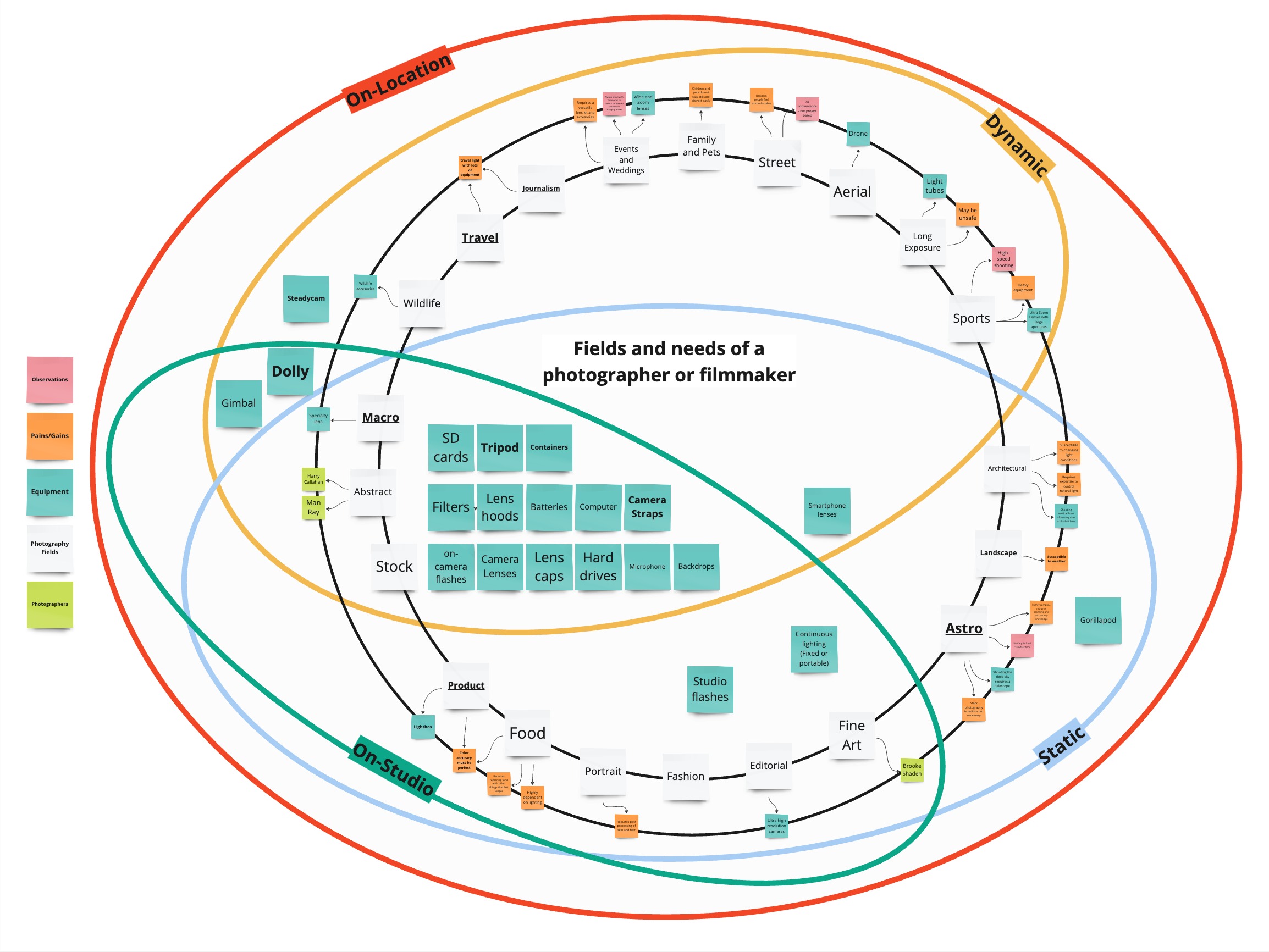
In parallel, a complementary research approach involved collaborating with a seasoned professional in the filmmaking industry to gain insights into prevailing industry demands, existing solutions, and potential areas for innovation. Luc Forsyth, a highly respected cinematographer and director based in Toronto, Canada, boasting nearly 15 years of diverse international experience spanning five continents, was chosen as a focal point for this exploration. Through his esteemed YouTube channel, Luc offers invaluable insights into his workflow, preferred equipment, documentary resources, and career advice for budding filmmakers. Drawing from his extensive online content, an overview of his relationship with the film medium was meticulously documented in Figure 2.
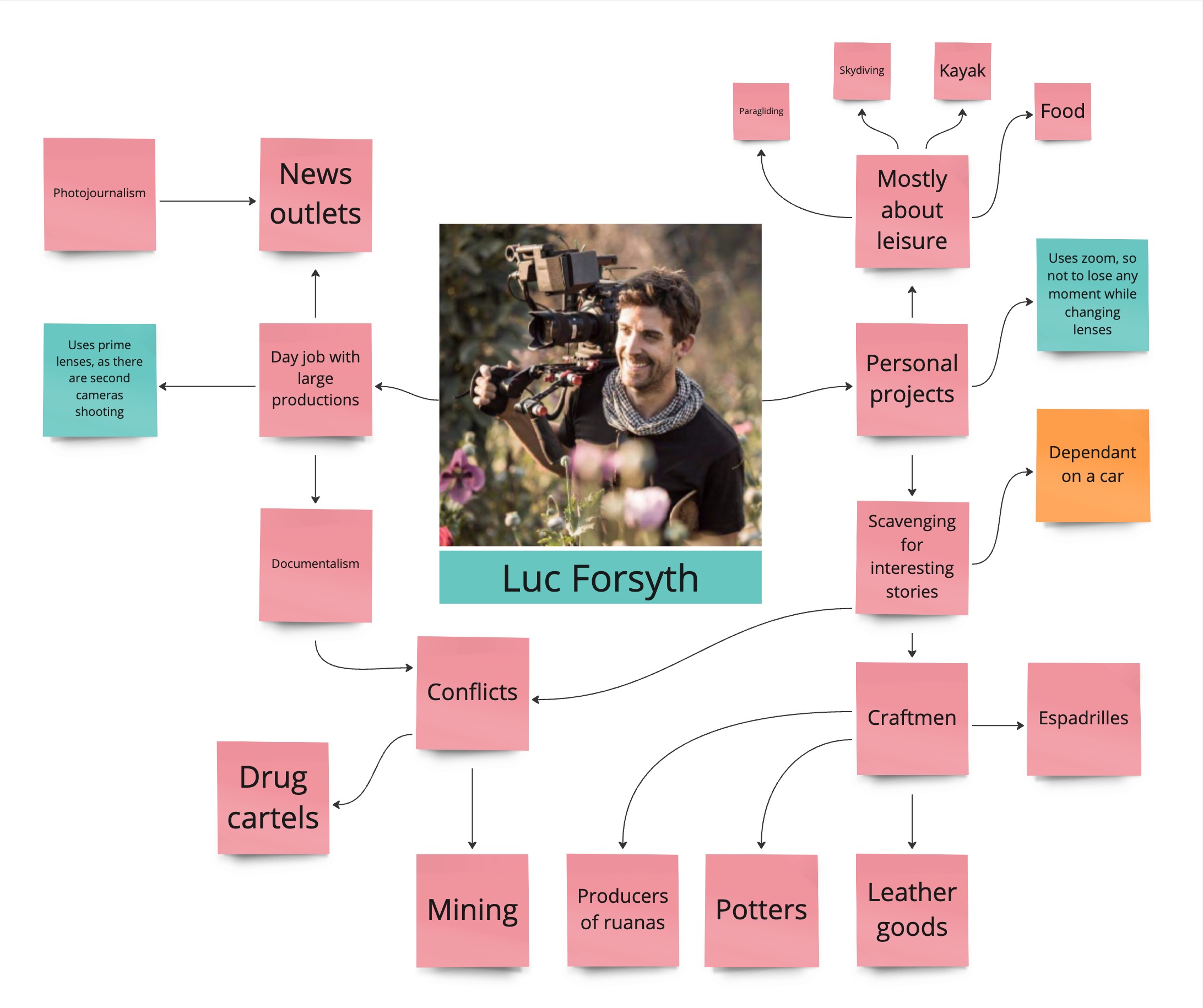
Furthermore, Luc's intricate workflow, encompassing his systematic approach to film production, was meticulously captured and analyzed, culminating in the detailed depiction provided in Figure 3. It includes the gear he uses in each stage of the production process.
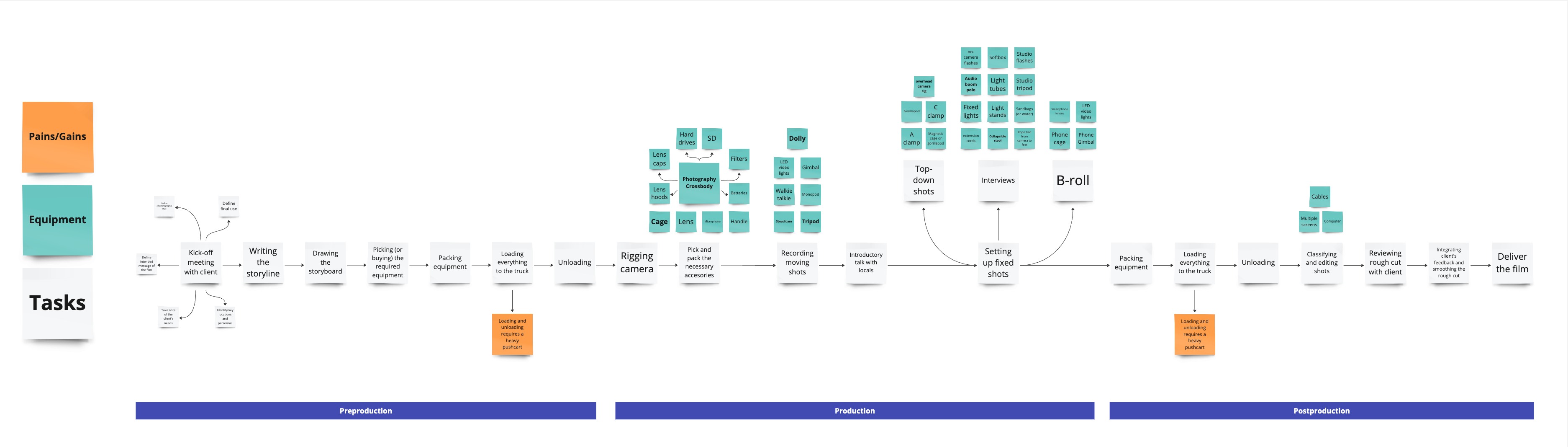
Exploration of opportunities
After research, opportunities were explored, focusing on purely mechanical devices without mechatronics. Developing an electromechanical system was out of scope for this project for budget and timing reasons and also required careful consideration of electrical and software compatibility.
These opportunities turned into product categories that could be reinvented with new exciting features, improved in usability or performance, or redesigned to fill a gap in the consumer market. These included products like dollies, tripods, Steadicams, collapsible stools and containers, crossbody bags, and rigging equipment, chosen for their compatibility and ingenious mechanical behavior.
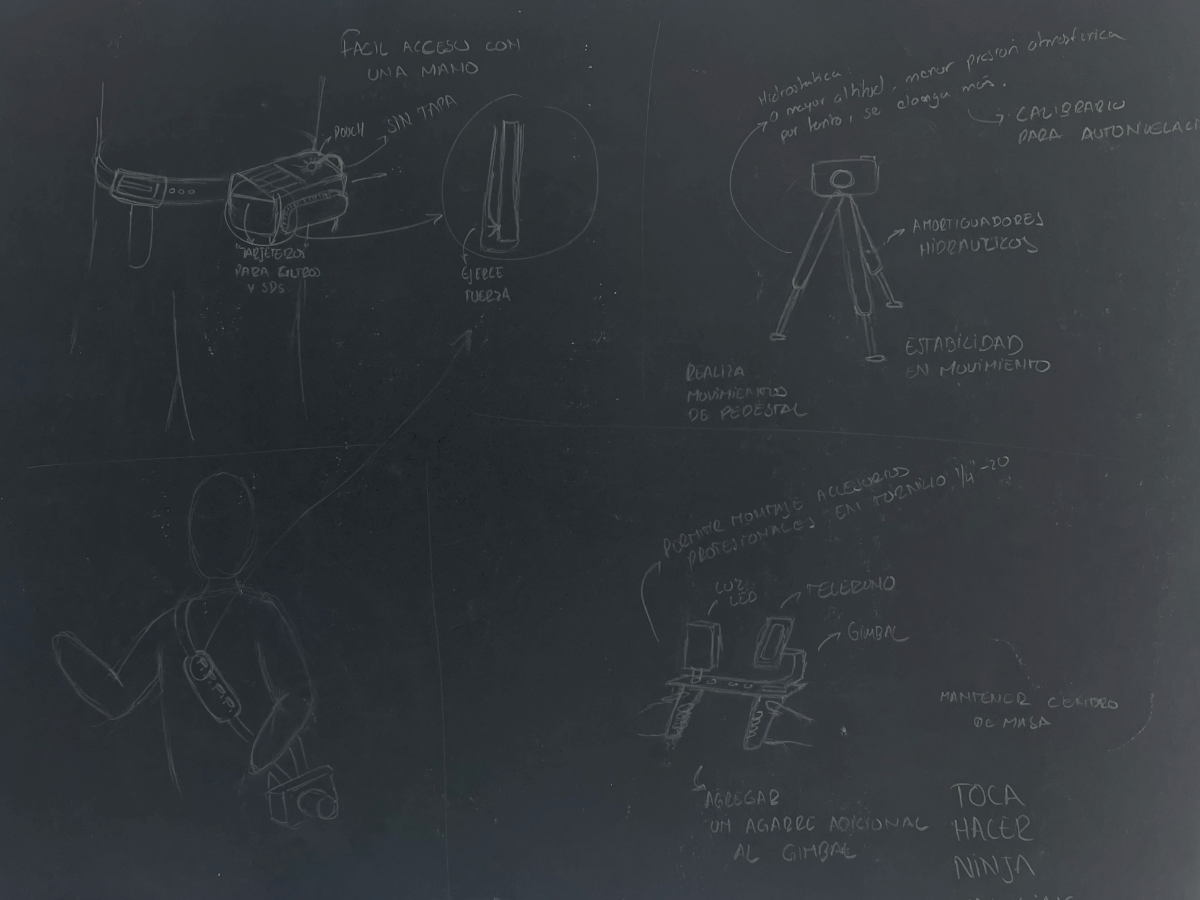
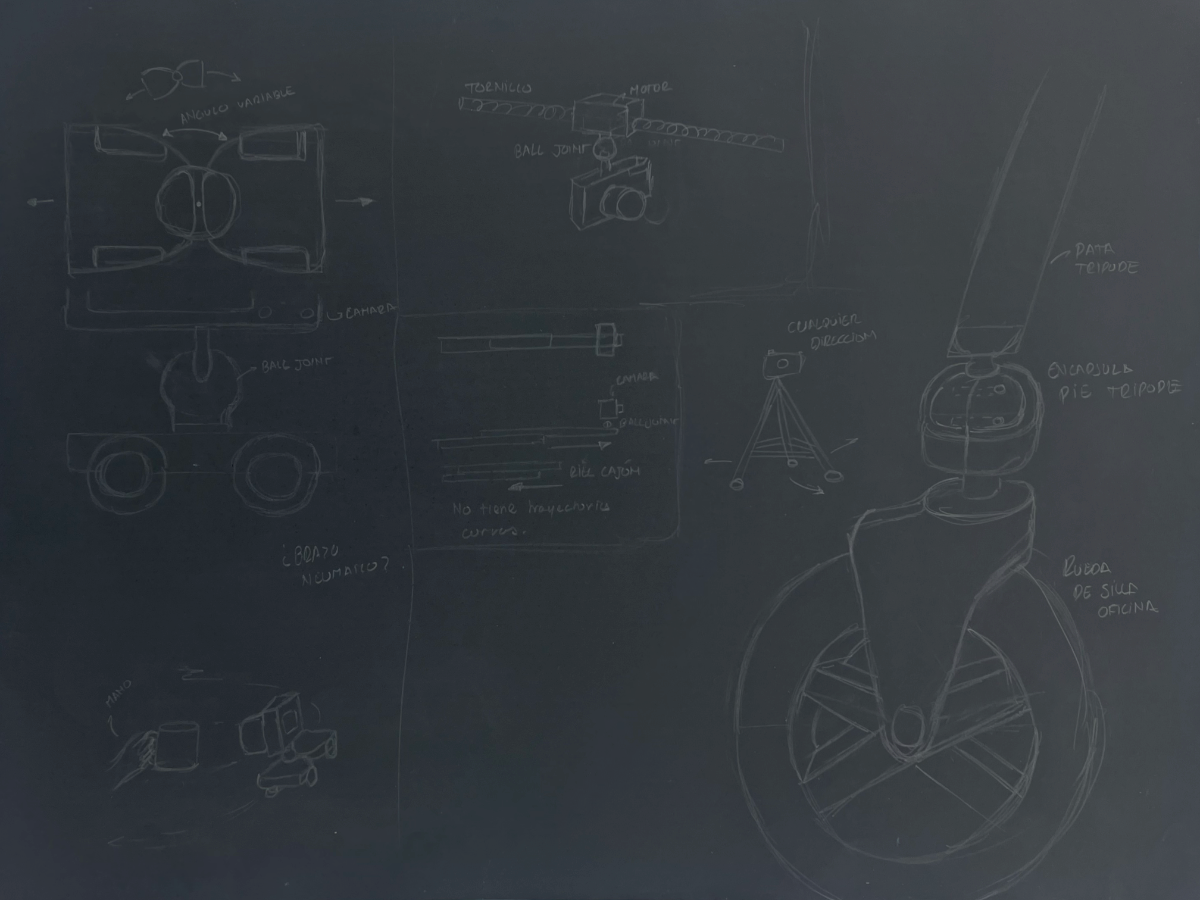
Opportunity definition
Content creators want to capture professional-quality video, but the devices used by the film industry don’t fit their production budget or style. One of the biggest limitations is the smoothness with which they can perform camera movements without having such equipment, as vertical vibrations caused by the cameraman’s walk often disrupt the shot.
Competitor benchmarking
Many products already on the market, ranging from professional gear to consumer goods, state they smooth camera movement compared to handheld shooting. The most popular, the smartphone gimbal, doesn’t reduce vertical vibrations. The most affordable option that dampens vertical movements is the DJI Ronin 4D, which price keeps it out of the consumer and even prosumer market.
Thus, the product’s differential value is to add vertical dampening to the smartphone Gimbal, turning it into a prosumer-level DJI Ronin 4D without the need for additional batteries and absurd price tags.
Product Definition
Dampher aims to eliminate video jitter caused by walking. It provides a low-cost, lightweight solution compatible with prosumer gear that is easy to transport and use, bridging the gap between consumer and prosumer filmmaking equipment.
Mechanical Design
The design process begins with defining the system requirements. From this, the use cases and ways of interacting with the object were identified, as well as the relationships between the different mechanical components. The solution required a hybrid of a balanced arm structure (similar to a Luxo L-1 lamp) and a car damper.
The proposed system is—in essence—a mechanism of four bars joined by pins and restricted in its diagonal by a spring. Its proper functioning depends on the spring’s force and on smooth sliding on the pins, which in turn depends on the system's dimensions.
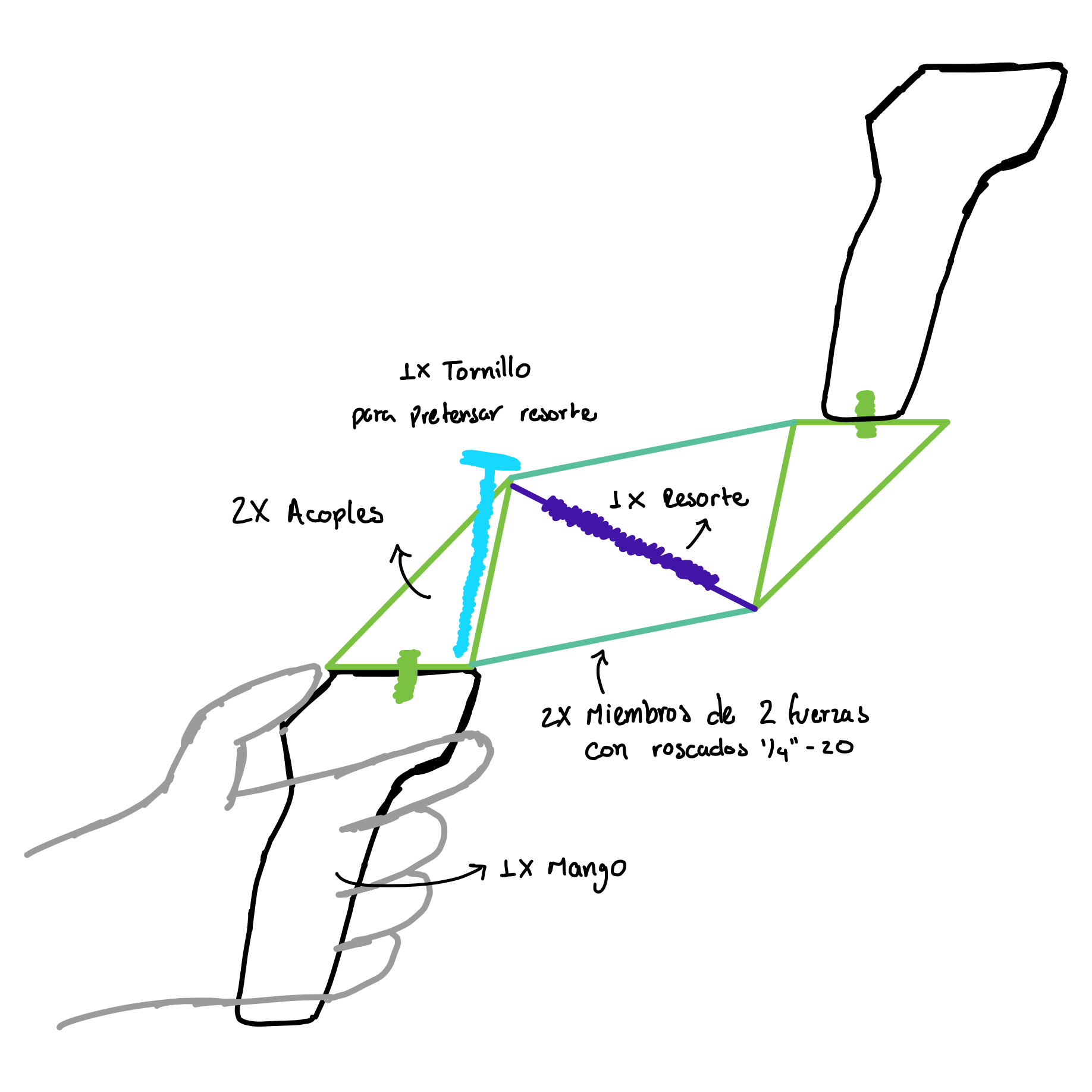
Mechanical Engineering
The engineering process behind Dampher began with identifying the forces the device would encounter in various use case scenarios. This involved estimating internal forces affecting components, particularly the spring. A simulation was then coded to determine the optimal dimensions of each component to minimize user effort and internal stresses. The spring was manufactured according to the specifications derived from this simulation.
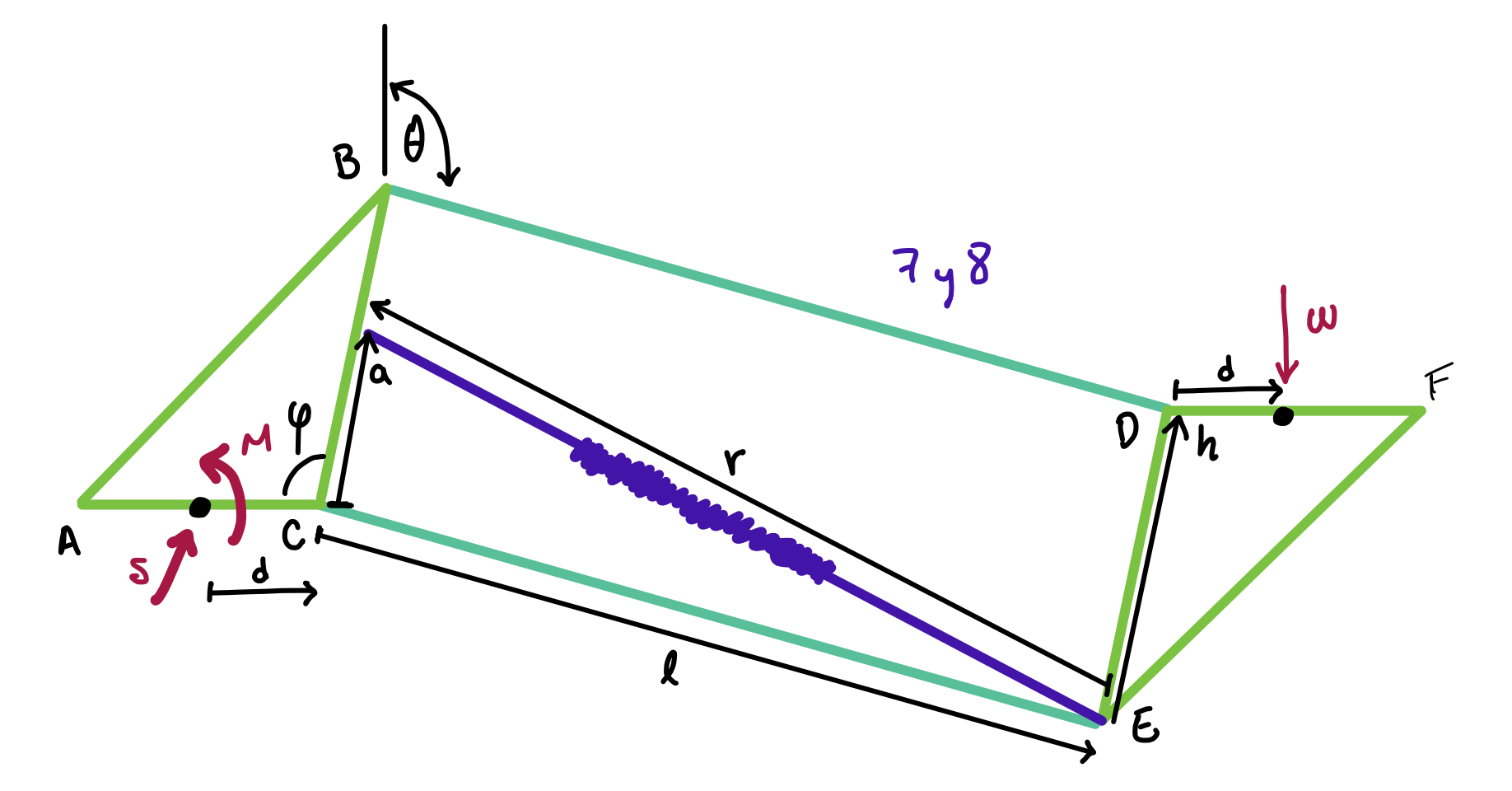
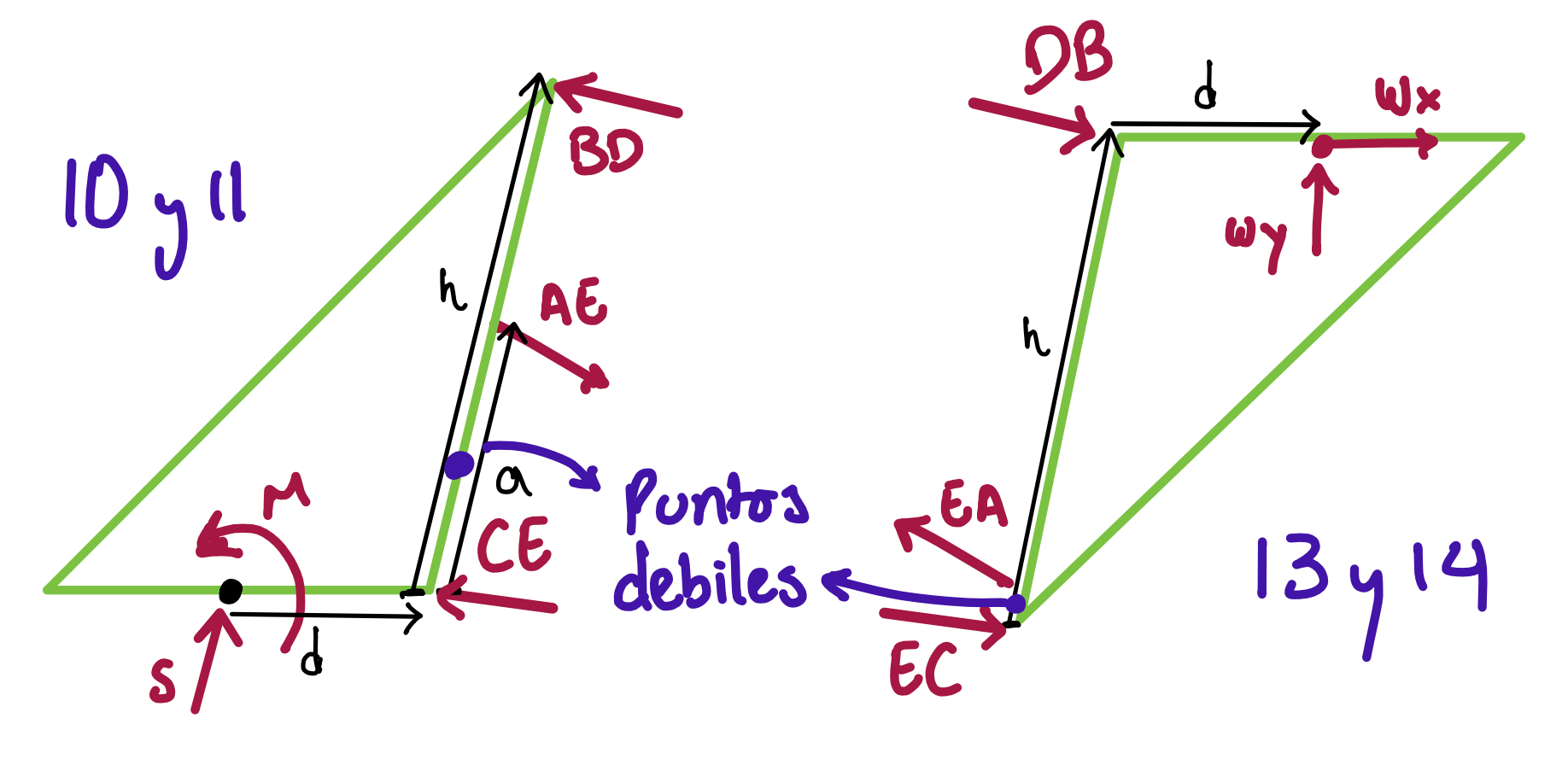
The force analysis was conducted on the core device and its two main components, illustrated in Figures 7 and 8. These free-body diagrams provided unique insights into the forces at play. While some forces in Figure 8 were considered internal forces in Figure 7, they still influenced the device's performance, necessitating a comprehensive analysis.
These diagrams were translated into vector equations and implemented into a MATLAB simulation, varying all dimensions shown in Figures 7 and 8. The initial results highlighted two additional unknown variables: the natural frequency of vibrations exerted on the camera by the cameraman's movements and the natural frequency of the spring. These were experimentally measured for all use cases and multiple speeds using accelerometers and laboratory equipment. The first unknown was measured experimentally for all use cases (shown at the product landing) and for multiple speeds using a phone with an accelerometer, and for the second unknown with a laboratory montage, a video camera, and a few weights.
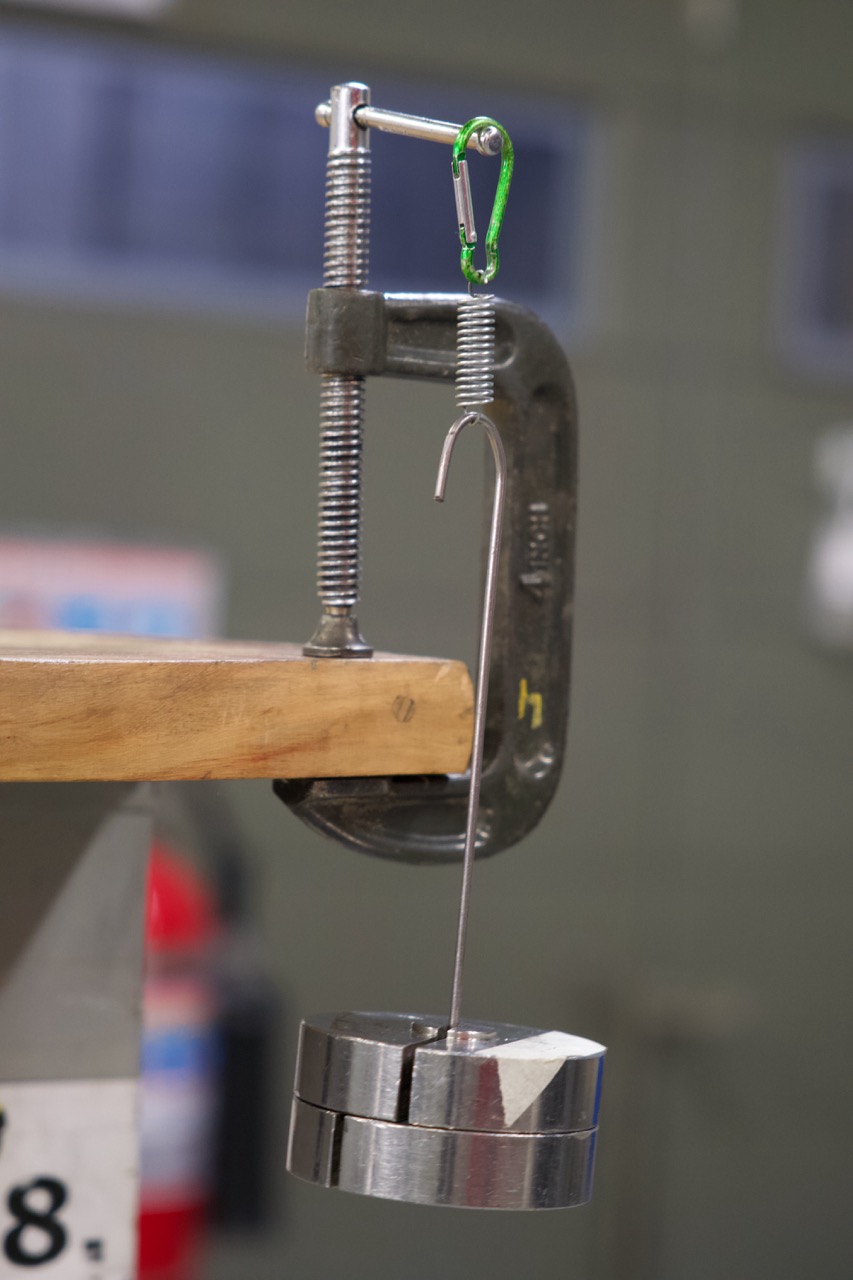
Integrating the experimental data into the MATLAB model generated various graphs illustrating each dimension's impact on the system's behavior. This iterative process allowed for informed design decisions to optimize Dampher's performance and user experience.
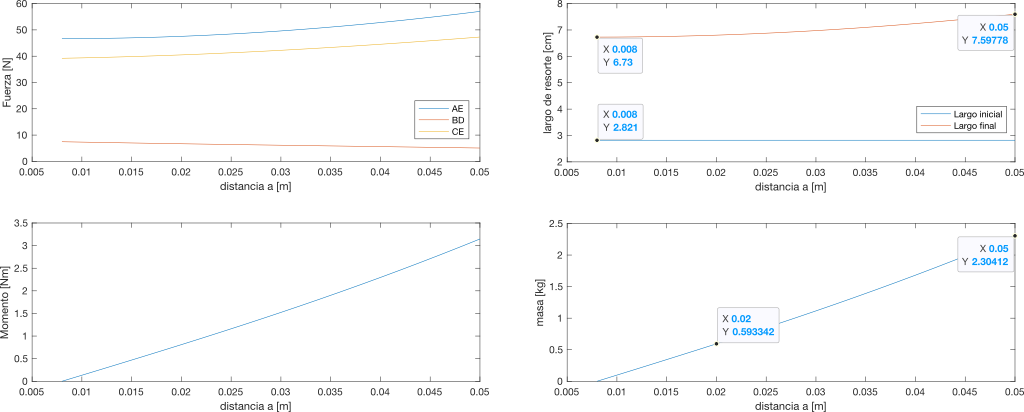
User Testing
A V1 prototype was created for user testing using dimensions derived from the MATLAB code. Feedback indicated comfort and ease for shooting high and eye-level angles, with the user's hand at an appropriate angle. However, shooting lower angles proved difficult and uncomfortable, requiring the device to be held closer to the ground. Consequently, adding a second handle location was deemed necessary to facilitate varied body positions and shooting angles.
An ergonomic and biomechanical analysis revealed the need to minimize the horizontal distance between the camera and the handle to alleviate stress on the user's hand and wrist, particularly reducing side effects on the carpal tunnel. Adjustments were made to certain dimensions, and the MATLAB simulation was rerun with these considerations.
Form development and CMF design
The revised dimensions from user testing led to creating a V2 prototype, focusing on minor adaptations to enhance stability by widening attachment surfaces, increasing safety by rounding all edges, and adding visual interest and force symmetry to the final product.
.jpeg)

The CMF (Color, Material, and Finish) design for V2 commenced by aligning Dampher's association with strength, stability, and a dynamic lifestyle. This translated into a color scheme featuring shades of blue and green, symbolizing these attributes. The characteristic color gradient of Dampher was developed to vary according to the device's morphology, reflecting its intimate relationship with the CMYK FDM 3D printing process. It thus isn’t a linear gradient, as shown in Figure 17. PLA was chosen as the material due to its availability for color mixing, facilitating the creation of the desired gradient.
.jpeg)
DxAM: Design for Additive Manufacturing
Throughout the design process, the chosen manufacturing method introduced specific constraints that were carefully addressed. Dampher necessitates bolted joints with the camera or gimbal, yet 3D-printed threads are inherently weak. To mitigate this issue, components were divided to allow for the embedding of hex nuts where necessary and to minimize overhangs that could increase the process's failure rate. These design adaptations are illustrated in Figure 18.
