Introducing our innovative cooking pan with a removable handle, designed to revolutionize your kitchen experience! After extensive research and analysis, we've crafted a product that seamlessly blends functionality with practicality, catering to the needs of modern living spaces.
Key Features and Benefits:
- Versatile Usage: From oven to stove to table, our pan effortlessly transitions, eliminating the need for multiple dishes.
- Space-Saving Design: With its removable handle, our pan not only saves space during use but also makes storage and dishwasher cleaning a breeze.
- Sustainable Solution: A shared handle between multiple pans reduces material usage, promoting sustainability.
- Premium Quality: Crafted with high-quality materials, our pan ensures durability and reliability for everyday cooking needs.
Target Market:
Ideal for individuals living in tiny homes, RVs, or shared spaces, our pan caters to the compact lifestyle without compromising on functionality. However, its benefits extend to larger households seeking efficiency and convenience in the kitchen.
Market Trends:
With the cookware market witnessing steady growth, fueled by the rising demand for modular kitchen solutions and improved living standards, our product aligns perfectly with evolving consumer preferences.
Competitive Edge:
While other pans with removable handles exist in the market, we've addressed common issues highlighted by users, such as handle durability and attachment ease, ensuring an enhanced user experience.
Customer Needs:
Following Kano's Model of Customer Satisfaction, our pan not only fulfills basic requirements like even cooking and safety but also incorporates excitement features such as hassle-free handle attachment and a convenient spoon rest. Additionally, performance features like one-handed operation and rust resistance enhance the overall usability and longevity of our product.
Experience the future of cooking convenience with our innovative cooking pan with a removable handle. Say goodbye to clutter and hello to effortless cooking!
Project Definition
Introduction
The integration of compliant mechanisms in product design marks a transformative approach within the engineering industry. Compliant mechanisms, which rely on flexible component deflection to generate motion and force, promise numerous benefits such as enhanced structural efficiency, usability, and aesthetics. This project explores the implementation of these mechanisms in a consumer product, highlighting the synergy between form and function.
Motivations
The project aims to:
- Embrace unconventional engineering design.
- Develop innovative conceptual products.
- Integrate design thinking into mechanical design.
- Ensure ease of manufacturability.
- Draw inspiration from nature for engineering solutions.
Brief and Objectives
General Objective:
Design and build a consumer product using a compliant mechanism.
Specific Objectives:
1. Identify a consumer product that benefits structurally, usability-wise, or aesthetically from a compliant mechanism redesign.
2. Understand the behavior and parameters of compliant mechanisms.
3. Develop concepts fulfilling the product’s functions with compliant mechanisms.
4. Create a realistic proof-of-concept prototype from early concepts.
Research Question
How can early design concepts be translated into realistic proof-of-concept prototypes using compliant mechanisms?
State of the art
A compliant mechanism is a mechanism that makes use of elasticity to provide at least some motion and force. Such elasticity comes from the “deflection of flexible members rather than from movable joints only.” [2]
Main advantages
· Increased Performance: High-precision movements, low weight, and low-friction joints.
· Lower Costs: Simplified manufacturing and reduced part count.
· Simpler Construction: Potential for miniaturization and planar fabrication.
Main disadvantages
· Limited Motion: Constraints from deflecting member strength.
· Design Challenges: Simultaneous consideration of motion and force behavior.
· Fatigue Life and Stress Relaxation: Cyclic loading and creep in polymers must be managed.
Methodology
The project follows five main milestones:
- Product Definition: Evaluate and select a consumer product for compliant mechanism redesign.
- Experimentation: Benchmark and test compliant mechanisms to understand functionality.
- Research: Investigate modeling approaches, materials, and design parameters.
- Concept Design: Develop and evaluate concepts for the product’s functions.
- Prototyping: Create proof-of-concept prototypes using additive manufacturing.
Outcomes, Scope, and Limitations
The project aims to produce a proof-of-concept consumer product, contribute to academic knowledge, and compile comprehensive documentation. Constraints include the use of specific 3D printing equipment and adhering to university intellectual property regulations.
Ethical Considerations
The project poses no risk to participants or conflicts of interest, ensuring ethical integrity in its execution.
Product Definition
After a systematic selection process involving a benchmark of various consumer goods, a specific product has been selected for detailed investigation and development, guided by predefined criteria aligned with project objectives and the advantages of compliant mechanisms.
Selection methodology
Definition of criteria
The first step in defining the product was establishing criteria based on the advantages and disadvantages of compliant mechanisms and the objectives outlined in the project proposal. Each criterion was assigned a weight to prioritize its significance in the evaluation process. These criteria serve as guidelines for assessing potential products and mechanisms.
· Product Relevance: Frequency of use, excitement, perceived value, and innovation potential. Weight: 70
· Benefits of Compliance on UX: Aesthetics, ergonomic force transmission, volume reduction, ease of use, low vibration/noise, lightweight. Weight: 35
· Benefits of Compliance on Product Cycle: Efficiency, precision, cost-effectiveness, maintenance, ease of construction and manufacturing. Weight: 18
· Limitations: Superiority of digital solutions, size constraints, competition with industrial machinery. Weight: -115
· Challenges: Mechanical loading requirements, linear force-movement dependency. Weight: -60
· Difficulties: Continuous rotational motion, fatigue, stress relaxation. Weight: -15
Exploration phase
In the exploration phase, various tools were utilized to identify potential products suitable for integrating compliant mechanisms. This involved researching existing products in the market and visiting multiple retailers catering to relevant audiences. Additionally, products and tools essential for the identified product archetypes were explored to understand their relevance, viability, and pertinence to be redesigned into a compliant mechanism.
Tool #1: User archetypes
Starting with a list of archetypes, a brief literature search on their activities was performed. A list of items they might need was composed for each activity, gathering information from casual conversations with people who perform said activities.
Tool #2: Market inspiration
Possible retailers targeted to those audiences were identified and visited to document their product offerings. Local flea markets, furniture and kitchenware retailers, and concept stores were included with in-store and online shopping.
Benchmarking process
Following the exploration phase, a benchmark was conducted to evaluate potential products against the defined criteria. Each product was assessed based on compliance with the established criteria, with weights applied to prioritize critical features. This comparative analysis provided insights into each product's strengths and weaknesses, aiding the selection process.
The best-performing products were:
· Detachable Handle Pans: 7.22
· Buckle: 7.06
· Pull Down Shelf: 6.59
· Umbrella: 6.35
· Welding Auxiliary Clamp: 6.23
Chosen product
After thorough benchmarking, the product with the highest score emerged as the preferred choice for further development. The selected product is a cooking pan with a removable handle. This product not only showcases the potential for integrating compliant mechanisms but also addresses practical needs in the kitchen space, offering versatility and convenience to users.
Features and benefits
A cooking pan with a removable handle offers these main benefits to its users:
§ From kitchen to table, without the need to serve: It can be used in the oven, stove, and table.
§ Saves space when used, stored away, and inside the dishwashing machine.
§ A shared handle between multiple pans uses less material than a handle per pan.
Current and future market trends
The product audience is people with tiny homes or RVs, but it’s not limited to these profiles as the benefits listed before also apply to larger homes, although with lesser value for the user.
“The total addressable market (TAM) for cookware was valued at USD 23.73 billion in 2021. It is estimated to reach USD 41.12 billion by 2030, growing at a CAGR of 6.3% during the forecast period (2022-2030).” [7]
Competitors analysis
Several types of pans available in the market come with removable handles and offer similar benefits. These pans have varying prices, materials, and mechanisms. Five different online offerings were chosen based on their unique mechanisms and evaluated based on their price, materials, mechanisms, and rating on the retailer's website to benchmark the pans. Most of these pans had a Bakelite handle and a grip-like attachment mechanism but differed in their locking mechanisms and body material. Carote and Tefal are the only ones to claim that their handles can hold up to 10kg.
User Reviews and Comments
· Issues with insufficient handles, difficulty in attaching/removing, and melting or flimsy handles.
· Comments from Core77 Design magazine highlighted similar issues
Functional analysis
The proposed device’s main function is to allow the user to move hot pans easily while saving space. This can be achieved through 4 subfunctions:
· Closing Trigger: Transfer force to grab the pan. Must not interfere with the standard use sequence.
· Main Spring: Provide strength and resistance. Should have two stable equilibrium positions.
· Pan Interface: Restrict all 6 degrees of freedom of the pan relative to the handle.
· Opening Trigger: Transfer force to release the pan. Should provide feedback regarding the system's state.
Stakeholder’s needs
· Basic Features: No damage during regular use, secure attachment, even cooking, dishwasher safe, hold at least 10kg.
· Excitement Features: No additional step to secure the handle, non-proprietary attachment system, exchangeable handles, a place for a cooking spoon, feedback on open/close.
· Performance Features: Long-lasting strength, jam-resistant, easy to clean, lightweight, rust-resistant, easy attachment/detachment.
Quality Function Deployment
Stakeholder’s needs and engineering specifications were correlated using a QFD (Quality Function Deployment), through which the most relevant engineering specifications were identified:
Product definition
The functional analysis and the QFD results yielded key product characteristics regarding the 4 subsystems and the materials they would be made from. These findings must be considered during the design and prototyping phases.
Subsystems
· Closing Trigger: Must not require additional movement from the user. The required movement must be natural and intuitive.
· Main Spring: Must come from a bistable mechanism that provides the auto-locking feature and stability.
· Pan Interface: Must restrict all 6 degrees of freedom of the pan relative to the handle while staying as far away from the heat source as possible.
· Opening Trigger: Must react to an atypical yet ergonomic movement that applies a medium force onto the trigger. Must provide feedback on system state.
Material Choice
The material must be highly resilient, readily available, resistant to temperatures of at least 100°C, and compatible with FDM 3D printers. For its heat resistance and flexibility, the chosen material is a copolymer of Nylon 6 and Nylon 6.6 (PolyMide CoPA).
Experimentation
This section details the process of selecting and benchmarking examples of compliant mechanisms and testing their functionality through 3D printing to understand mechanical compliance and the effects of the manufacturing process on these mechanisms.
Mechanical Compliance
Reference mechanisms
To explore compliant mechanisms, three examples were selected and benchmarked based on their functionality and design particulars:
Material and Process Characterization
Material: Polymaker PolyMide CoPA, a 3D printing filament copolymer of Polyamide 6 and Polyamide 6.6, which is hygroscopic and requires drying before processing to ensure good structure, layer adhesion, and appearance.
Moisture Conditioning: To achieve desired properties, the material must be conditioned to 70% relative humidity and ambient temperature for 15 days or alternatively submerged in boiling water for accelerated moisture absorption.
Characterization Goals: Assess the effect of treatment time on tensile and flexural strength and deviation in tensile strength due to manufacturing variability.
Design of Experiments
Three experiments were designed to collect necessary data:
1. Deviation in Tensile Strength: Five identical specimens, conditioned per manufacturer's recommendations, tested for tensile strength following ASTM standards.
2. Effect of Treatment Time on Tensile Strength: Three specimens submerged in boiling water for 5, 15, and 30 minutes, respectively, tested for tensile strength following ASTM standards.
3. Effect of Treatment Time on Flexural Strength: Four specimens submerged in boiling water for 5, 15, and 30 minutes, respectively, with one specimen conditioned per manufacturer's recommendations, tested for flexural strength following ASTM standards.
Separate experiments for tensile and flexural strength tests were conducted to avoid increased project cost and labor, staying within project scope.
Manufacturing Procedure
Drying
Filament dried at 70°C for at least 12 hours until relative humidity dropped below 20%.
Printing
Specimens are printed in a single batch per type following the manufacturer's suggestions and technical standards.
· Tensile Specimens: 2 perimeters, 4 solid top and bottom layers, 100% cubic infill.
· Flexural Specimens: Perimeters only, printed at 255°C nozzle temperature, 200mm/s speed, 0.2mm layer height.
Moisturizing
· Conditioned Specimens: Left at ambient temperature (20°C) and humidity (50%) for 15 days.
· Treated Specimens: Submerged in boiling water for specified treatment times.
Results
All tensile tests exhibit a brittle fracture, falling below the manufacturer's indicated yield stress. The sample that most closely resembles the expected behavior was the one that underwent the 5-minute treatment.
The flexural samples showed a fragile fracture when conditioned and a ductile one when treated. Only the 5-minute treatment yielded results that fell within the manufacturer’s interval.
Analysis
The tensile tests revealed that the 5-minute treatment led to the highest tensile strength, while no heat treatment resulted in the expected ductile behavior, leaving all specimens fragile. It was noted that as treatment time increased, strength decreased, and a more ductile behavior was produced. Furthermore, the impact of heat treatment diminished with longer treatment times, suggesting that the specimens reached a saturation point. Ultimately, only the specimen treated for 5 minutes exhibited the expected ductile behavior and yield stress, as longer treatments resulted in yield stresses below the anticipated range.
Conclusions
The optimal treatment time of 5 minutes balanced increased tensile and flexural strength with reduced fragility, ensuring safe and effective user performance. Exposure to a combination of hot water and vapor effectively modified mechanical properties to match TDS values.
Concept Design
This section explores the morphology of the four subsystems identified in the functional analysis, detailing potential shapes and structures for each subfunction.
Morphology exploration per subfunctions
The functional analysis decomposed the device into 4 subsystems, each one responsible of one of the subfunctions of the device. These subsystems
Closing trigger: Act on the mechanism to close the grip
Grip Spring: Store and transmit force
Pan Interface: Securely attach the pan and hold its weight
Opening trigger: Act on the mechanism to open the grip
Design Concepts
Testing
Chosen concept
The bending arm concept was chosen for its small deformation, predictable behavior, and potential fine-tuning. Variations of the design with various lengths of flexures and bending arms were designed, manufactured, and tested empirically.
The first working prototype has only one pair of flexures: a bending arm that opens and closes the Pan Interface by pushing/pulling on it and a cantilever beam on the underside of the handle that pulls the mechanism into its closed state.
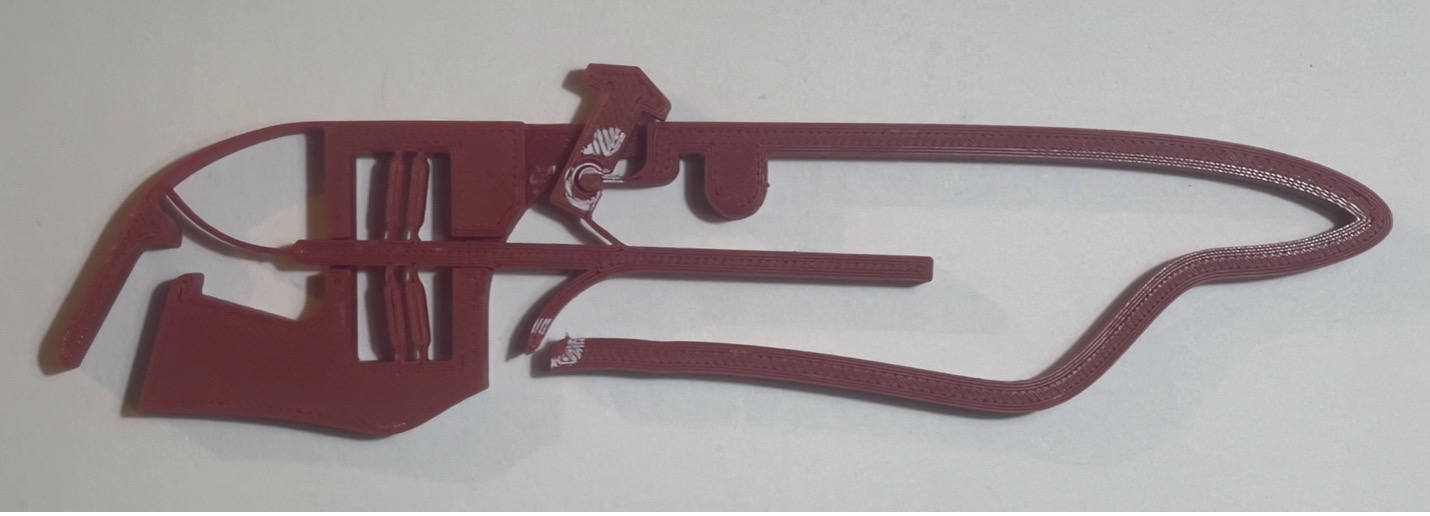
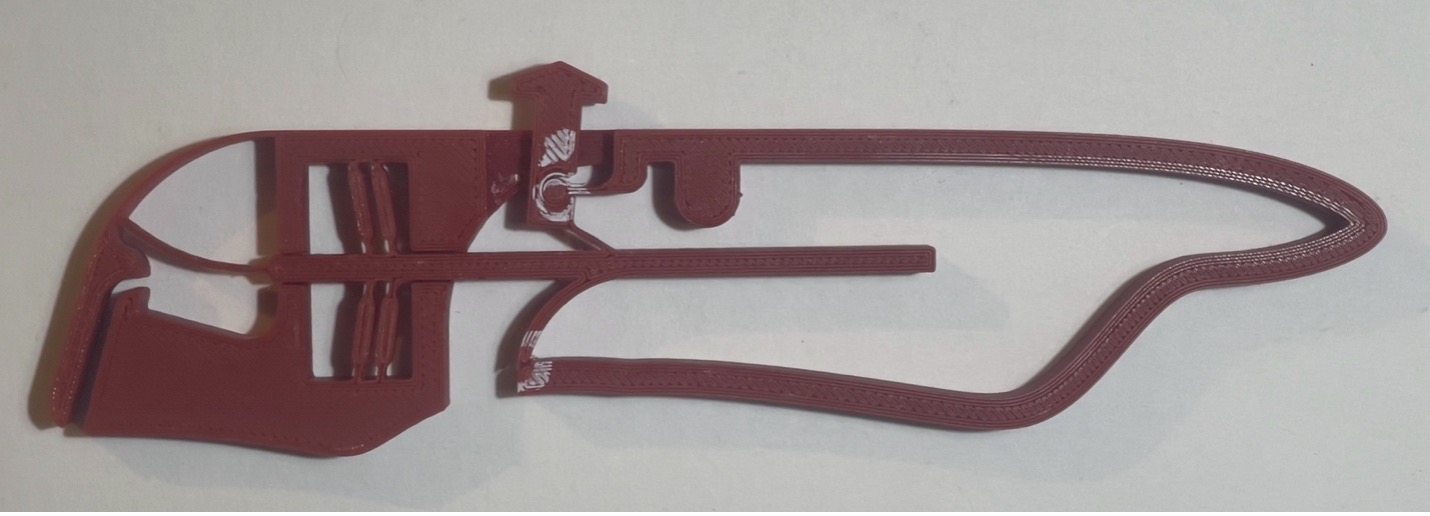